Rise of the humanoids: How robots are transforming the warehousing industry
"Humanoids were once fantastical elements in science fiction but have found their way into real-world settings."
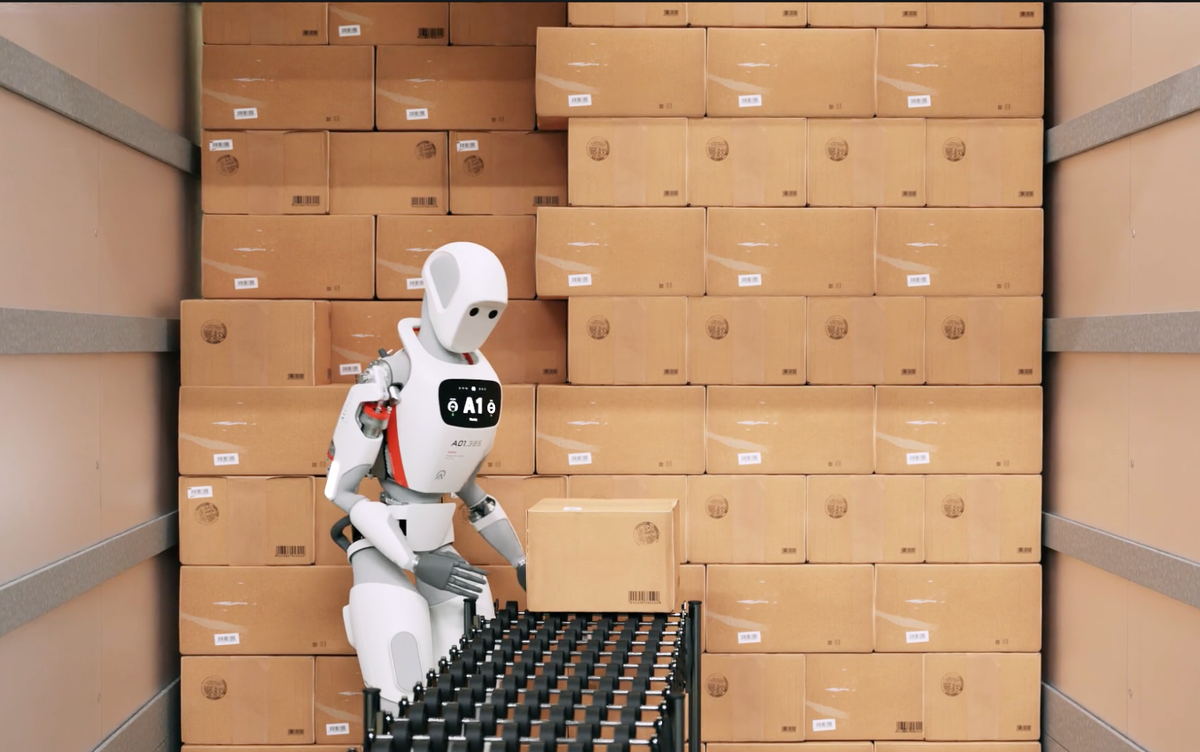
In the past, automation was perceived primarily as a remedy for labour shortages. Today, that’s no longer the case. With intelligent automation systems like humanoids blurring the line between creative ambition and tangible application, warehouses are presented with an unprecedented opportunity to reclaim the human ingenuity once lost to repetitive, monotonous tasks.
Warehouse automation has undergone several bouts of evolution, each time becoming more advanced, sophisticated, and integrated into a broader ecosystem of human and machine collaboration. The humanoid robot market is projected to grow from $2.03 billion in 2024 to $13.25 billion by 2029 at a CAGR of 45.5%, reflecting the increasing demand for intelligent systems capable of transforming industries.
Strategic integration of automation
Automation is not a silver bullet for workforce challenges - it’s only as good as the strategy behind its implementation. The right solution, placed to solve a correctly identified problem, can unlock productivity to levels unimaginable before, but if misapplied, it can lead to wasted resources, worker frustration, and a disconnect between technology and actual business needs.
When it comes to solving the labour shortage problem, warehouses must look within to identify the problem areas as well as outside to understand broader dynamics, such as demographic shifts, skill gaps, and the changing nature of work. For example, as the ageing population shrinks the available workforce, the rise of the gig economy is creating a demand for more flexible, short-term work arrangements.
External factors such as these affect how warehouses need to plan for automation. Just filling positions doesn’t cut it anymore; addressing the long-term viability of operations and adapting to the evolving workforce landscape is more important than ever before. If there is an apparent lack of interest in a specific role, it’s crucial to understand why. If warehouses want to attract young, creative talent, they need to focus on the how. How can warehouses create an environment that nurtures innovation and meets the needs of this demographic? Where does automation fit into all this? How can the fear of labour displacement make way for exciting new opportunities?
Automation’s role as a workforce enhancer should take precedence over its potential as a replacement tool. When integrated thoughtfully, technology of this level of sophistication can enhance safety, job satisfaction, and well-being in warehouses. Consider the potential of human-humanoid collaboration in mitigating occupational PTSD, particularly in high-stress environments where dangerous working conditions are common.
This not only reduces human exposure to hazardous tasks and repetitive, high-risk duties, but also enables workers to focus on less strenuous tasks that require higher cognitive engagement. Additionally, capabilities like real-time stress monitoring lower the risk of burnout and long-term psychological trauma.
The next frontier in labour automation
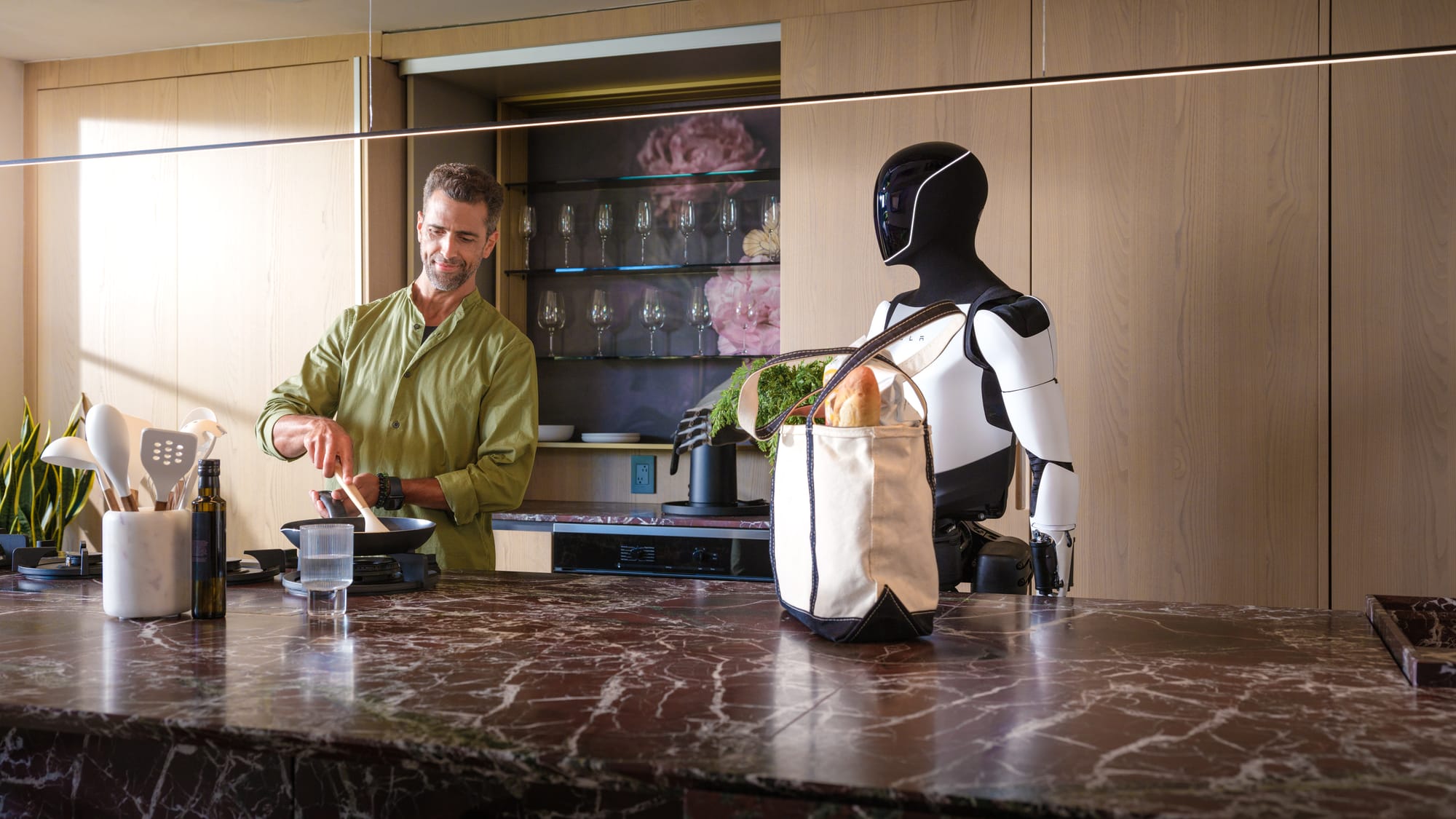
If humanoids were once fantastical elements in science fiction, today they have found their way into real-world settings, and are transforming industries. From manufacturing to healthcare and beyond, humanoids are changing the way workflows are designed, problems are solved and interactions are conducted. It’s no longer a stretch of the imagination - Amazon’s Digit, Tesla’s Optimus, and Apptronik’s Apollo are the forerunners of a new era.
Equipped with AI and advanced mobility to navigate around human coworkers and handle tasks that range from moving boxes to sorting items, these robots are designed to handle repetitive and physically demanding jobs such as item picking and unloading trailers. Their human-like movements, adaptability, and the ability to interact with dynamic environments make humanoids desirable for warehouse floors in the face of pressing labour shortages.
However, warehouses must carefully evaluate where humanoids can genuinely deliver the value that justifies their substantial investment. If the objective is to save time by minimizing walking distances, a conveyor system can handle this well. Similarly, if the aim is to quickly stack boxes, specialized robots like pick-and-place arms or palletizers are potentially faster and more cost-effective compared to humanoids.
Having moved beyond such repetitive tasks, humanoid robots and AI can support, for instance, decision-making and dynamic task allocation, adapting to shifting priorities and unstructured environments. Additionally, they can be integrated into existing workflows during peak periods without necessitating major changes to infrastructure or layouts, and their versatility allows them to tackle a wide range of tasks.
Ultimately, automation needs to solve a specific problem. Humanoids could make a difference if they are integrated to fill gaps where specialized robotic systems and human labour fall short. With humanoids set to play a central role in supply chain and logistics in the days to come, warehouses need to find the right balance between humans, standard robotic automation systems and the next generation of robotics like humanoids.
As an impressive upgrade over standard robotic systems (which are already great at executing repetitive tasks), humanoid robots take efficiency several notches up with advanced perceptual capabilities, heuristic algorithmic management, and reinforcement learning, among other things.
Integrating humanoids into environments like warehouses originally designed for human workers, however, requires careful consideration and adaptation. Even as anthropomorphic mechanization has come a long way, humanoid interactions with existing systems and workers must be rigorously tested to ensure safety and synchronization. Needless to say, when it comes to any advanced form of automation, ethical concerns should be addressed, too, especially in matters of job displacement and the psychological safety of warehouse workers.
Reshaping industries and redefining the future of work
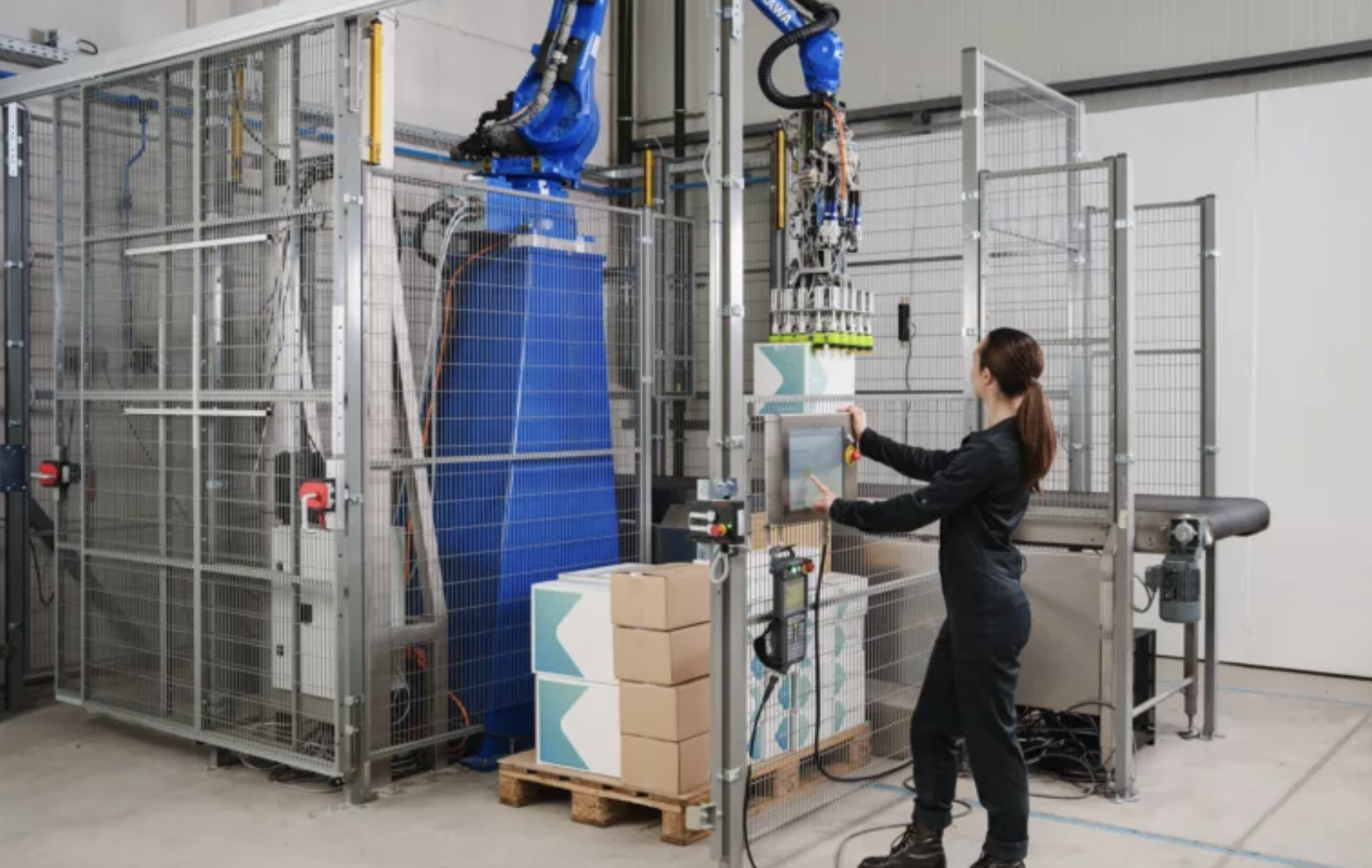
The goal isn’t just to stay ahead with the latest technology, but also to ensure operational functionality, stable flow of processes, and optimized workplaces. Above all, the real focus should be on how an industry like warehousing, which has long depended on human labour, can now elevate and empower workers to do more than repetitive, monotonous tasks.
The challenge lies in finding the sweet spot where automation can enhance precision and efficiency, and humans are liberated to contribute to innovation, strategic thinking and creative problem-solving.
While robotic arms, with their cost-effectiveness, speed, and precision, present the most appropriate choice for repetitive, high-volume logistics operations like picking-and-placing, humanoid robots, with their human-like mobility and interaction capabilities, are well-suited for workflows requiring adaptability or a human-centric approach. That said, it’s important to weigh whether the higher costs, complexity, and maintenance requirements of humanoids are justified, especially when robotic arms offer a more practical and efficient solution for most warehouse operations.
With technological advancements that can materialize human vision with utmost precision, we are stepping into a future where automation not only enhances human efficiency but also unlocks new human capabilities. Warehousing, along with other industries, will see the rise of new roles that allow human intuition, creativity and thought processes to shine. As automation and human potential converge, the possibilities are truly limitless.
Have you got a story to share? Get in touch and let us know.